切削加工最適化サービス
人と設備に依存しないモノづくり
(注)「切削加工精度向上サービス(旧名称)」
「切削加工最適化サービス(現名称)」
クラウドサービスでの技能伝承デジタル化「切削加工精度向上サービス(注)」
~切削前に製品品質の安定化と生産性向上を実現するNC補正技術~
株式会社日立ソリューションズ 粂野 紀忠
株式会社日立製作所 研究開発グループ 河野 一平
株式会社日立製作所 研究開発グループ 毛戸 康隆
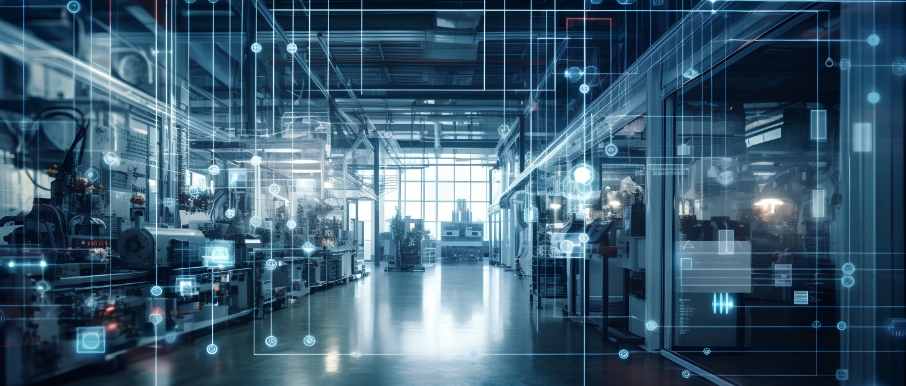
クラウドサービスにおける技能伝承デジタル化
「切削加工精度向上サービス」資料ダウンロード
はじめに
COVID-19や相次ぐ自然災害、地政学的リスクの高まりなどにより、製造業では製造や輸送の断絶によりサプライチェーンを頻繁に見直す必要に迫られている。このため、グローバルで安価に製造可能な拠点で集中生産する従来のグローバル生産体制から、どこででも生産可能な分散型の生産体制の構築が求められている。また、世界的に環境問題が大きく取り上げられ、気候変動対策として製造業のカーボンニュートラルが求められており、生産の省エネ化と再生可能エネルギーの利用が急速に進んでいる。今後もこの動きは進んでいくと考えられ、輸送最小化の観点から地産地消型のものづくりが拡大していくと考えられる。
これらの状況から、今後は地域に依存しないフレキシブルなものづくりが必要になると考えられる。すなわち、常に同じものを同じ方法で作り続けるのではなく、さまざまな製品の製造体制を素早く構築することが必要になる。このような変種変量の生産体制においては、以下の課題があると考える。
- 生産ラインの入れ替わり周期が短く、製造条件を十分に最適化できず、生産性や品質が不足する。
- 設備の過剰投資や低稼働率によりROA(Return on Asset)が低下する。
- さまざまな製品に対応可能な人材確保が難しい。
これらの課題に対して、製造ノウハウのデジタル化により「いつでも、どこでも、だれでも高品質な製造」が求められると考え、本サービスの提供に至った。製造現場では設備の特性を熟知し使いこなす熟練作業者のノウハウが重要である。製造設備特性をデジタル技術により定量化し生産設備に設定する加工条件を設備ごとに最適化することで高品質化を実現し、熟練オペレータや設備に依存することなく海外を含めた複数の拠点で同品質の製造を実現する「ものづくり」が可能になる。
工作機械の剛性を考慮した「たわみ補正」
日立の提供する切削加工精度向上サービスは、工作機械の特性を数値化して、加工経路や加工条件が記載されたNCデータを最適化し、加工品質の向上を狙うサービスである(図1)。加工品質の向上は単に加工品の精度向上を狙うだけでなく、現状の加工精度を維持したまま高能率な加工条件の適用を可能とし、加工時間の短縮やコスト削減にも貢献する。加工精度を悪化させる加工誤差の要因はさまざまあるが、切削加工精度向上サービスでは切削力による工具やワークのたわみに着目している。工具やワークのたわみは加工対象や工作機械によって変化し、個別の加工現場での対応が必要となるため、熟練作業者に依存して誤差を補正していた。そこで、切削加工精度向上サービスでは工具やワークのたわみを補正し、加工精度を向上させることを目的に、工作機械ごとに最適化された補正NCデータを生成する。本サービスはエンドミルによるミーリング加工と旋削バイトによるターニング加工を対象としている。ミーリング加工では工具のたわみに起因する加工誤差の補正を対象とし、ターニング加工ではワークのたわみを対象とする。工具のたわみはエンドミルだけでなく、エンドミルを把持するホルダや工作機械の主軸剛性によって決まる。同じ規格の主軸テーパであっても、工作機械の構造や経年劣化により主軸剛性には個体差があり、工作機械によって主軸の剛性値は大きく異なる。このような工作機械の個体差を考慮して加工パラメータの微調整(補正)を行うため、加工品質や加工開始までのリードタイムは作業者のスキルに依存する。そこで、工作機械の主軸剛性をテスト計測により数値化し、工具やホルダの形状に基づいて、工具先端の剛性を算出する物理モデルを構築した。テスト計測は工作機械の剛性を数値化するために1度測定すればよく、工具やホルダはCADモデルを入力することでさまざまなツーリングの組み合わせで剛性を毎回測定する必要はない。本モデルを切削シミュレーションに適用することで使用する工作機械の個体差に応じた加工誤差を高精度に予測し、補正値を考慮したNCデータを生成する技術を開発した。
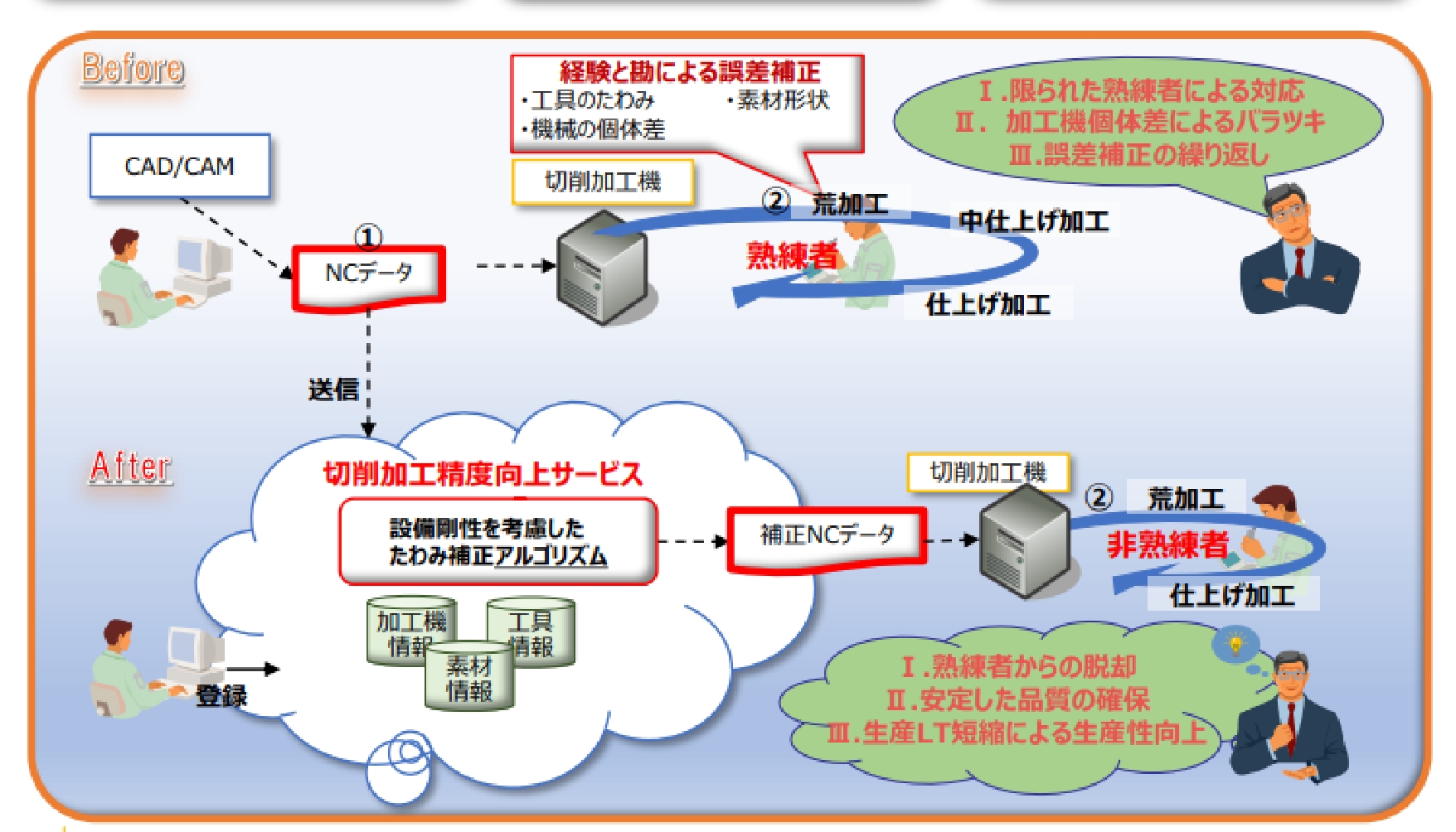
「送り速度の適正化」
本サービスに時間当りの加工体積や切削抵抗を送り速度の調整により平準化する送り速度の適正化機能を追加した(2022年5月提供開始)。CAMで作成したNCは、送り速度が一定であり、加工形状によっては加工負荷が少なく、工具の性能を十分に使い切っていない場合がある。また、一般に工具が材料と接触しないエアカットも多く含まれる。送り速度の適正化は、加工負荷が一定の値になるように送り速度を細かく設定する機能である。図2左に示すように、コーナ隅部などの加工負荷が大きい部分では送り速度を遅く設定し、切込みが小さく加工負荷が小さい部分では送り速度を速く設定する。これにより、加工負荷を一定の値に平準化することができる。更に、前述の工具たわみの補正機能と組み合せることで、加工精度の向上と加工時間の短縮を両立することが可能である。加工精度向上の観点では、工具たわみを平準化できるため、送り速度を一律で増加させるよりも加工誤差のばらつきが低減され、更なる高精度化が期待できる。また、加工時間短縮の観点では、加工負荷の大きい高速な加工条件でも工具たわみを補正できるため、工具のチッピングやびびり振動などの不具合が発生しない範囲での高速化が可能となる。
加工負荷は、時間当りの加工体積、切削力、工具のたわみを選択することが可能であり、工具ごとに任意に選択できる。例えば、荒加工用工具では、時間当りの加工体積や切削力を一定にすることで工具の折損を抑制しつつ、高能率化を図ることができる。また、中仕上工具では、工具のたわみを一定にすることで、仕上代を一定にする効果も期待できる。
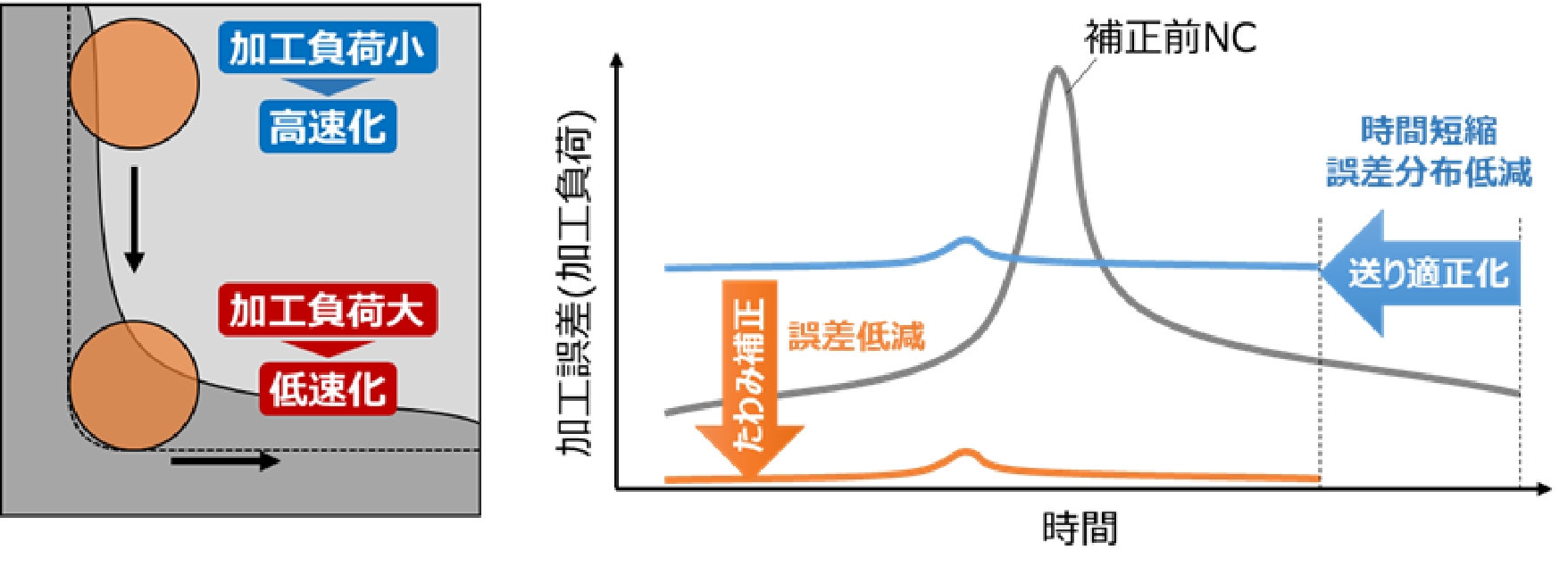
サービス概要
図3に切削加工精度向上サービスのシステム概要を示す。
サービス提供形態はWEBページを経由したクラウドサービスである。工作機械に関しては事前に剛性測定装置によりデータを取得、被削材の切削抵抗は切削実験によりデータを取得しDBを構築しておく。主軸剛性および切削抵抗の測定は、それぞれ専用の測定装置が必要になるため、測定サービスを提供している。また、主軸剛性測定単体でのサービス提供も対応しており、主軸剛性を定量的に評価することで、保有する工作機械の比較や経年劣化の把握に活用することも可能である。切削加工精度向上サービスとしては、専用のWEBページにアクセスし、必要なデータをアップロードするとWEBサーバー上で測定した主軸剛性および切削抵抗DBを参照して切削シミュレーションが実行され、対象の工作機械専用に最適調整された補正NCデータが生成される。生成された補正NCデータをダウンロードし、対象工作機械に適用することで高精度かつ高能率な加工を実現する。
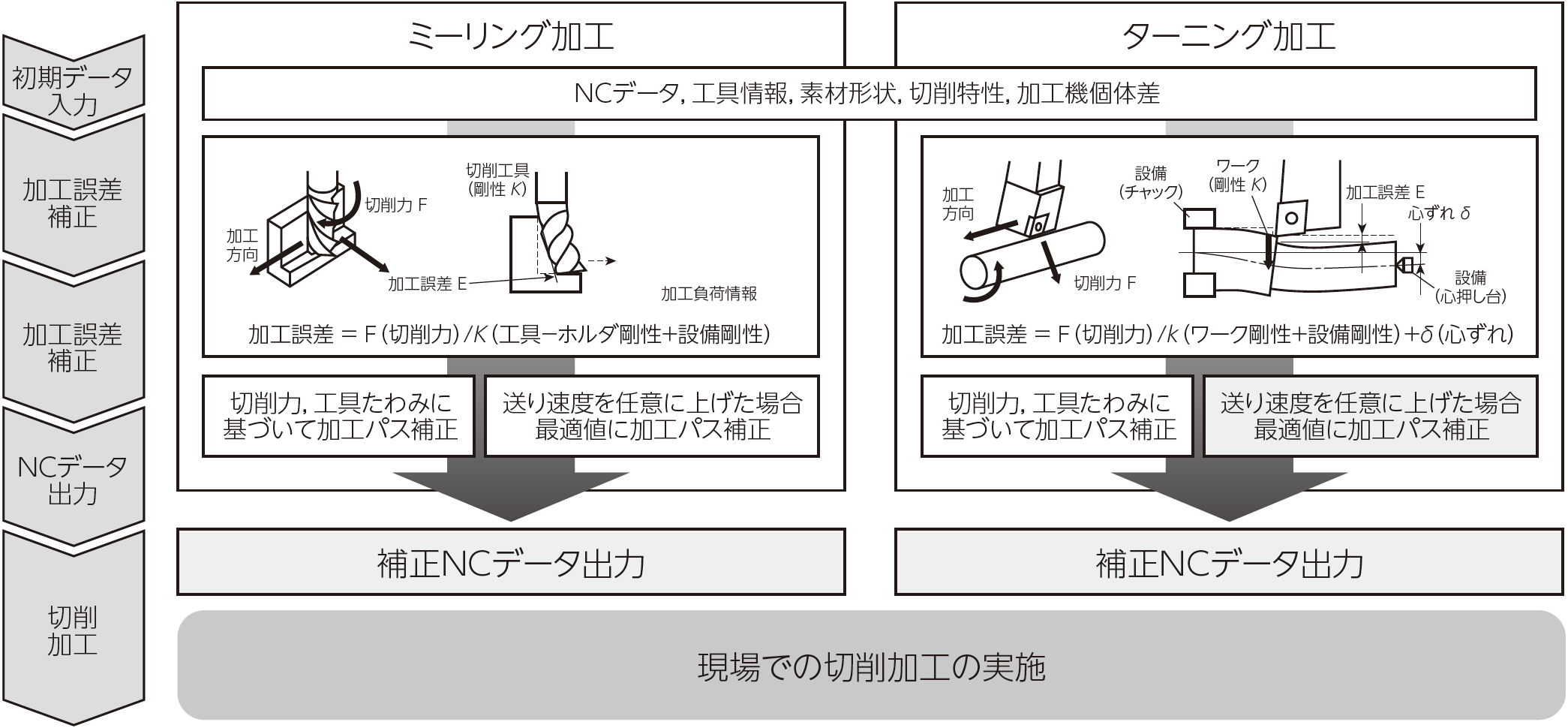
検証結果
(1)工具たわみ補正
図4に側面加工における工具たわみ補正の検証結果を示す。グラフの横軸は加工品形状の測定位置を示し、D1からD5は外幅、D6からD8は内幅である。また、縦軸は該測定位置での加工誤差を示す。各設備においてCAMで作成されたままの補正前NCデータでは、いずれの測定位置でも25µm以上の削り残しが発生した。一方、各工作機械に対して最適補正したNCデータを適用することで、いずれの測定位置でも加工誤差が大きく減少し、目標寸法に近づいた。補正しきれなかった加工誤差については、工作機械の位置決め精度などの要因が考えられる。(10年利用の設備で計測)
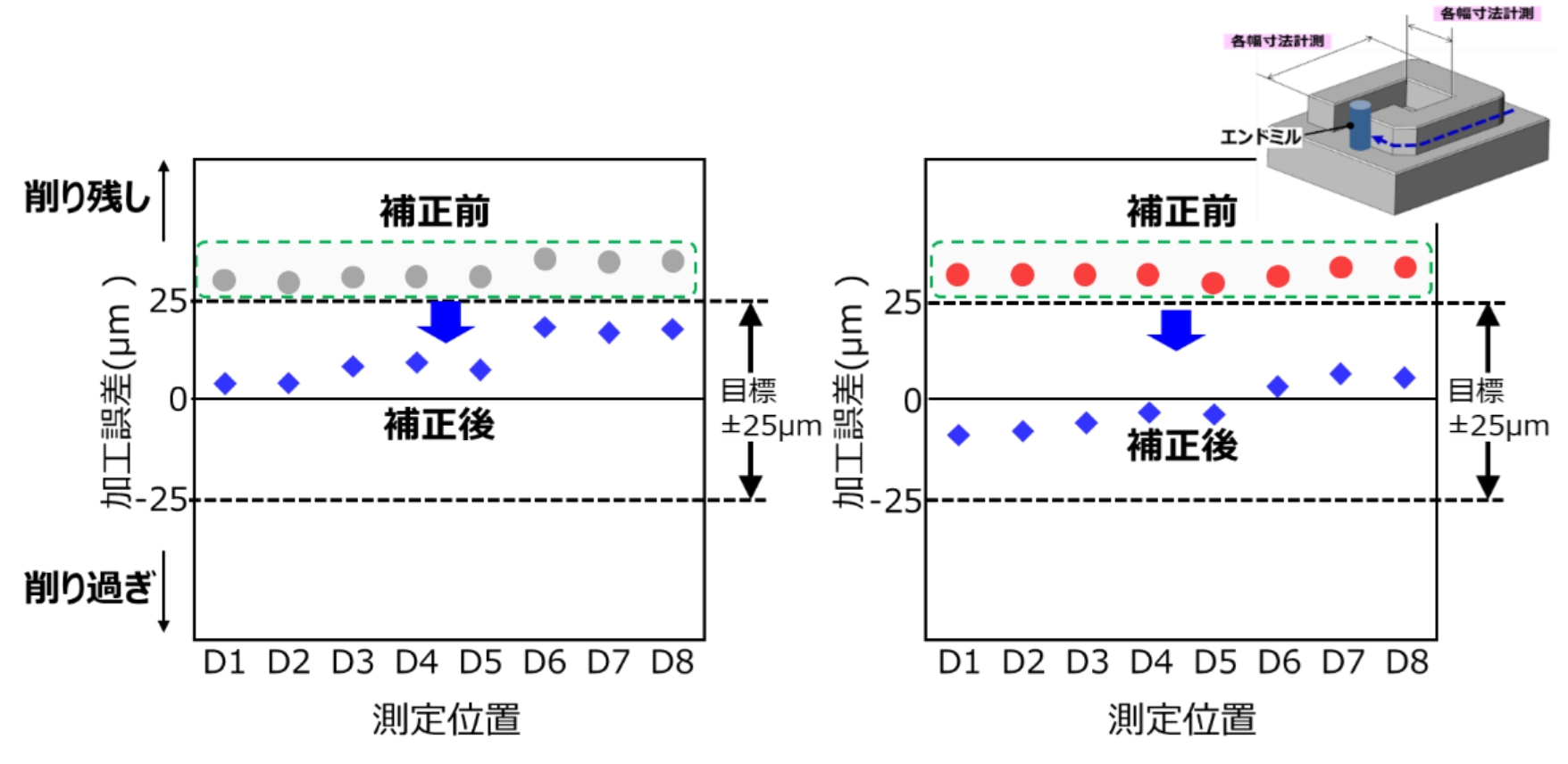
また、金型加工を想定して図5に示す曲面形状への適用効果を検証した。工具はボールエンドミルである。赤枠で囲った自由曲面部分について、従来のNCデータを使用した結果と補正NCデータを使用した結果の比較を示す。補正NCデータを適用することにより、誤差分布図から曲面全域にわたり、加工誤差の平均(14→2µm)とばらつき(43→18µm)が低減されたことがわかる。
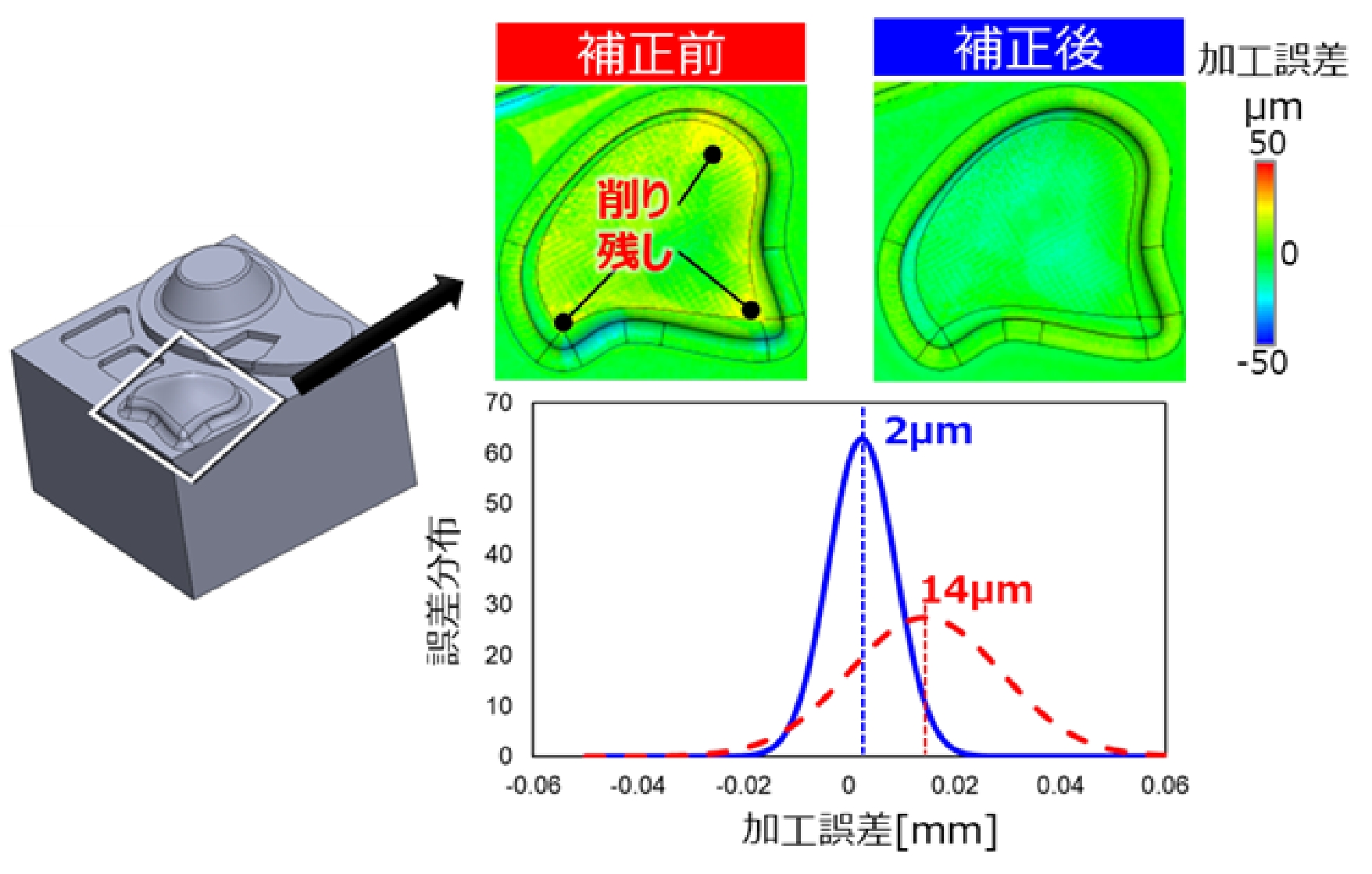
(3)送り速度適正化との併用
最後に工具たわみ補正に、送り速度の適正化を加えた検証について紹介する。図6に示す「H型」の凸形状を加工した。送り速度の適正化においては、時間当りの加工体積が一定になるように設定した。図6右上のグラフは各測定箇所の加工誤差を、右下の表は加工時間を示している。補正NCデータを適用することで加工誤差は平均90%低減され、加工時間は12%短縮された。このように、送り速度適正化を併用することで加工精度の向上と加工時間の短縮が両立できる。
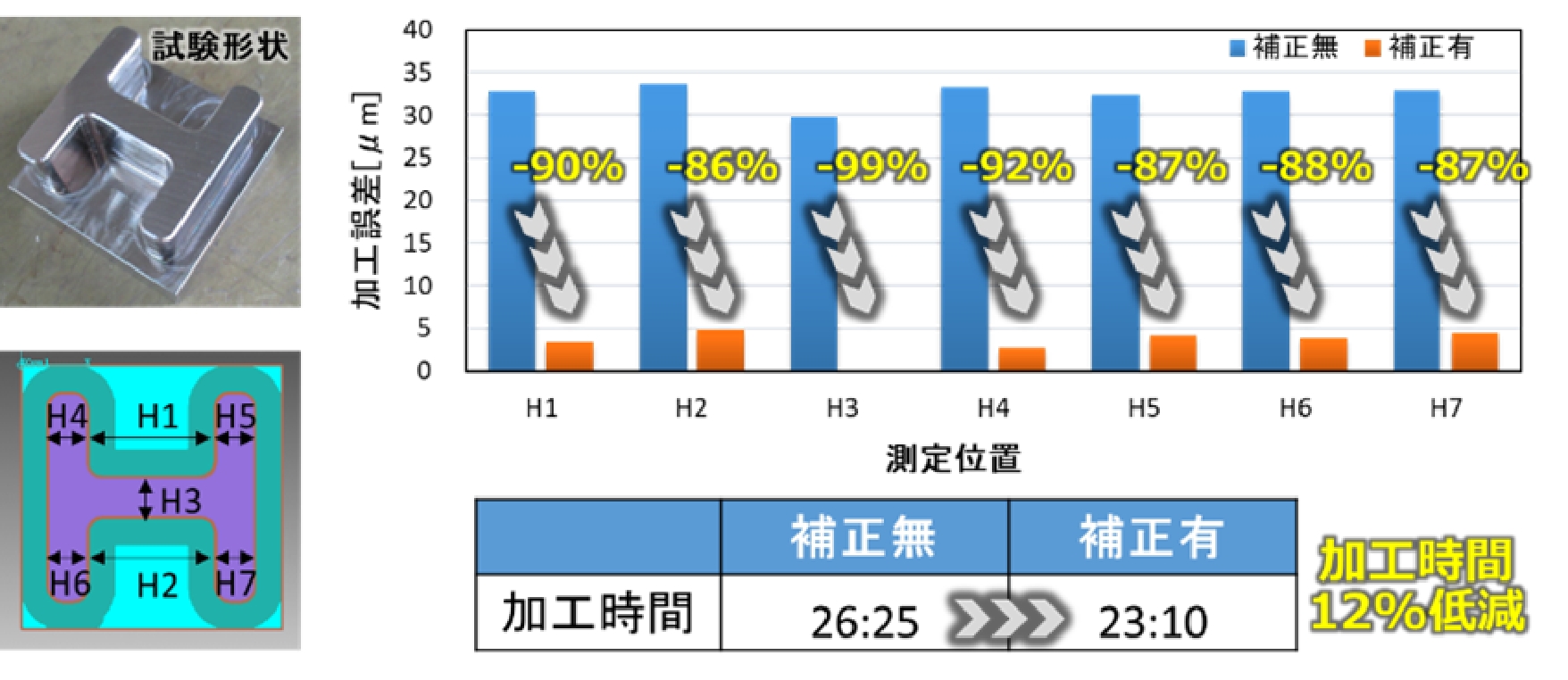
まとめ
切削加工精度向上サービスは、熟練者知見をデジタル化し切削前に品質を作り込む事でQCDへの貢献をめざしている。工作機械の設置環境による変化や剛性などの特徴に起因する個体差に合わせた加工パラメータの補正が可能であり、熟練オペレータの経験やノウハウに頼らず加工誤差が小さく品質が安定したものづくりを実現できる。また、加工品質の安定化だけでなく、加工時間の短縮にも貢献するサービスである。加工精度を向上させたい方、加工時間を短縮したい方はぜひ導入を検討いただきたい。